Customer profile
Damifo
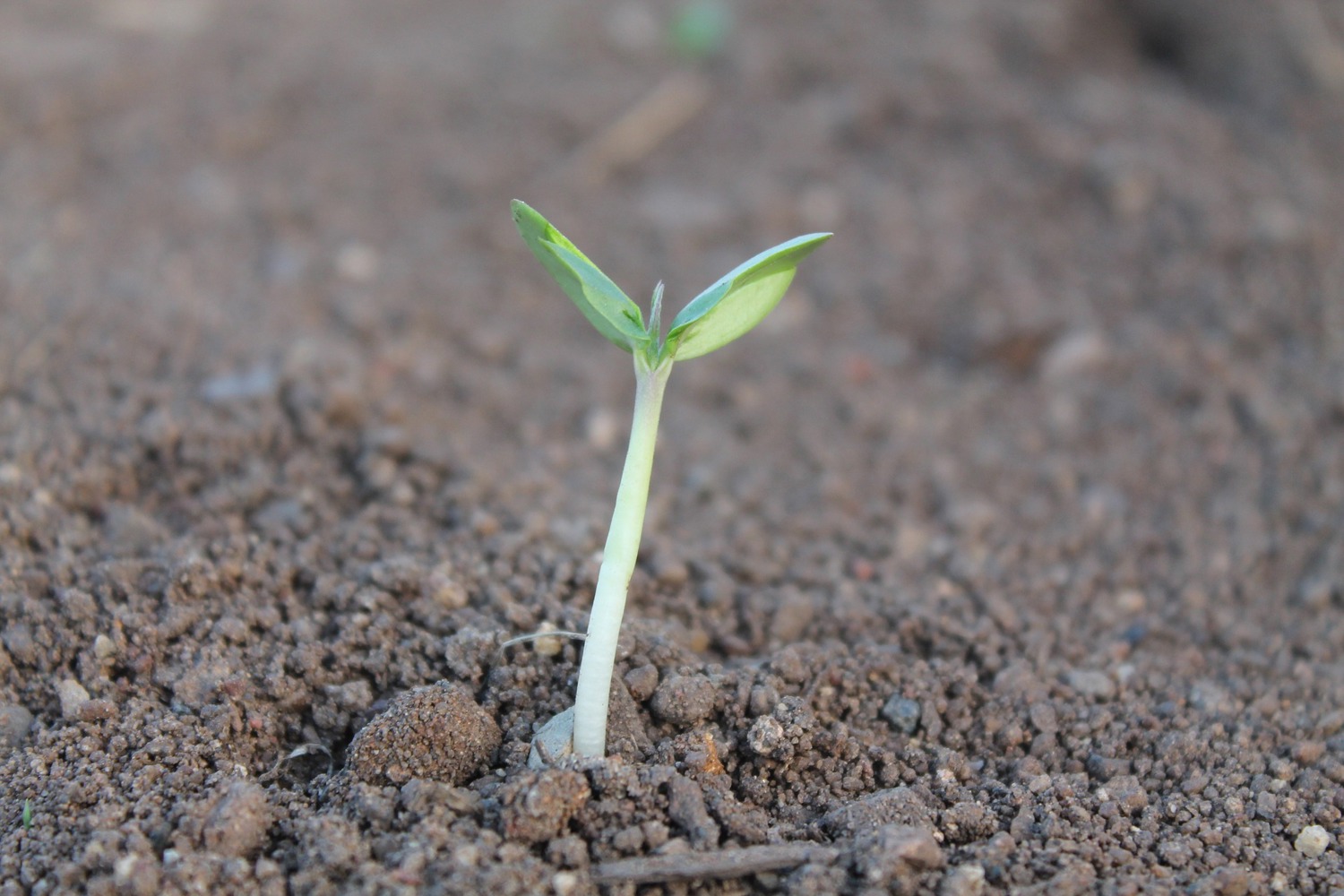
- Industry
- Waste Management
- Headquarter
- Hedehusene, Denmark
- Employees
- 25
- Market
- B2B
Platform Usage
CRM Batch Management Waybill Sampling UpcyclingCase Study
Golden Opportunity for Green AmbitionsWebsite
www.damifo.dkDamifo, founded in 2014 operates within the environmental, waste and recycling sector with collection, treatment, and upcycling of waste materials. The company has a solid track record of adapting and creating solutions where there is a need.
Damifo offers effective and innovative solutions for the construction, civil engineering and recycling industry. Damifo sees construction waste as a resource, and advocates sustainable recycling. It is the ambition that as much construction waste as possible is recycled into something useful rather than ending up in landfill. Therefore, the company has made it their specialty to accept materials from the construction and civil engineering industry, ensuring that it is handled efficiently and in ways that are environmentally sound.
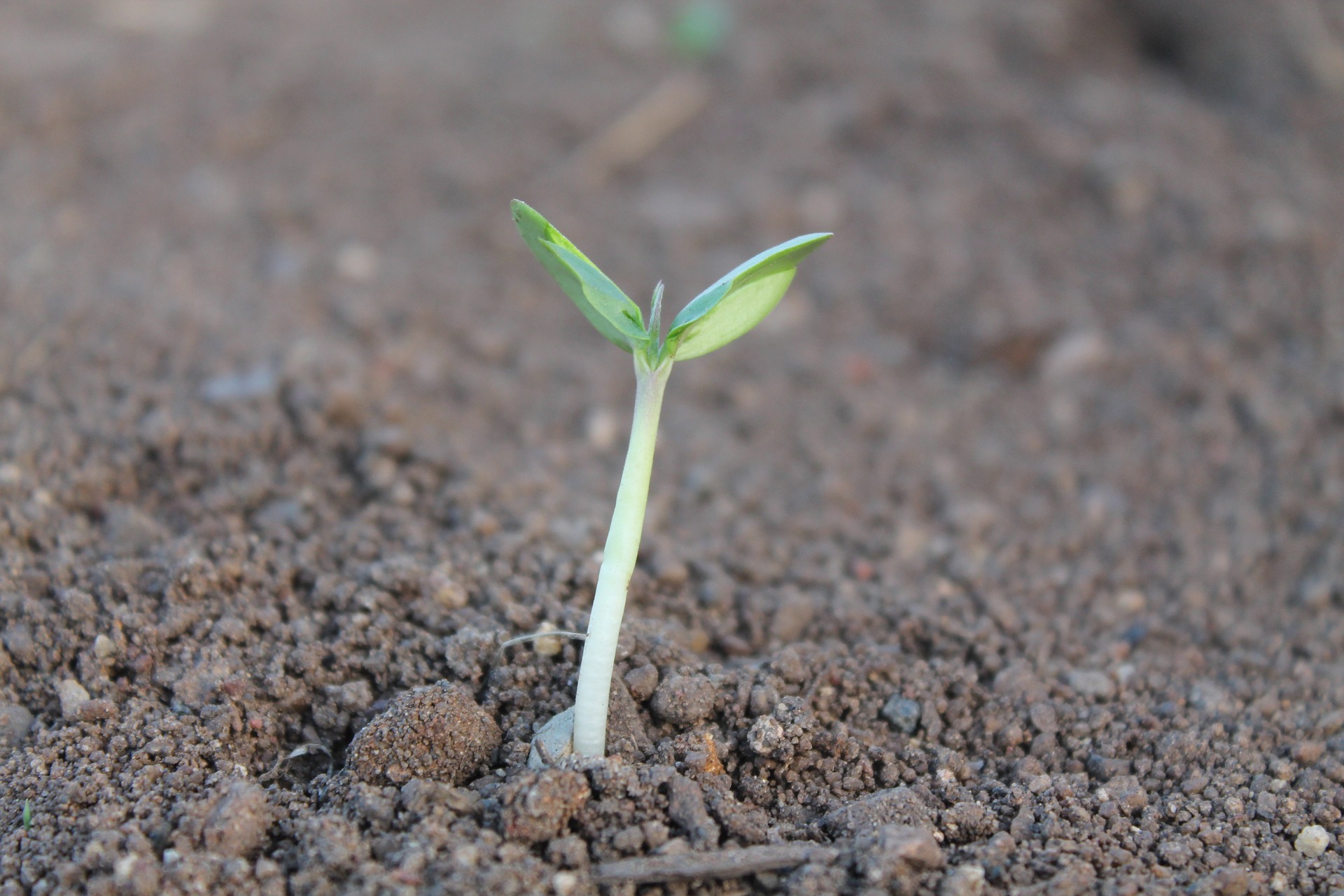
Damifo works to utilize available resources in a more intelligent and sustainable way. Ultimately, the goal is to recycle everything into something useful. Damifo was born directly into the circular economy. Based on the green transition in society, better resource utilization is the key element in the operation. Since 2014, the company has handled thousands of tons of waste that in many cases would have ended up in landfill.